HVAC INDUSTRY UPDATE
Changes in the HVAC Industry
The information about the HVAC Industry Changes was released by Trane. For more information, visit their website.
Industry Progress to Transition Away from High HFC
Refrigerants
Globally, the HVAC industry is working diligently to incorporate updated safety
standards into building codes as new products are commercialized to enable the next
generation, lower GWP refrigerants.
R-410A for chillers and other equipment will be replaced with alternatives that
have been described as having low flammability characteristics. These new
refrigerants have been widely tested and many of the smaller systems have
been in use for some time. As governments focus on building decarbonization
to achieve commitments under the Paris Agreement, the incorporation of highly
efficient, lower GWP electric heating equipment is a high priority, so innovation
in this space is significant. Trane is taking industry leadership in low GWP
electrification. More Information
Refrigerant Regulatory Evolution
The global scrutiny on refrigerants continues as there is continued focus on
sustainability, which has resulted in the development of lower global warming
potential (GWP), and next-generation options. This will help to offset the increasing global
demand for HVAC while continuing to reduce greenhouse gas emissions.
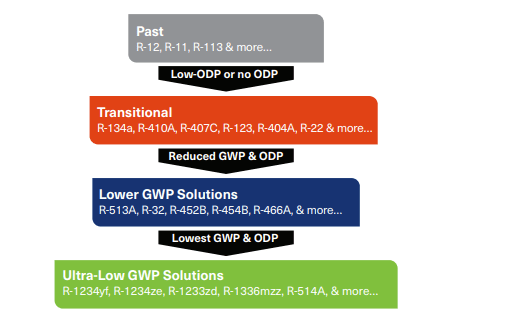
Global HFC Phase-Down Effective January 1, 2019
The 2016 Kigali Amendment to the Montreal Protocol phases down the supply of HFCs, as shown for
both Non-Article 5 (developed) nations and Article 5 (developing) nations. The European Union is shown
separately with their earlier and slightly different schedule.
The U.S. American Innovation and Manufacturing (AIM) Act mandates that EPA phase down the supply
of HFCs on the same schedule as the Kigali Amendment: 10 percent reduction now and 40 percent
reduction compared to the baseline in 2024. The AIM Act also authorizes EPA to require “Technology
Transitions” by limiting the global warming potential (GWP) of refrigerants for different types of
equipment. EPA Climate HFC Reduction
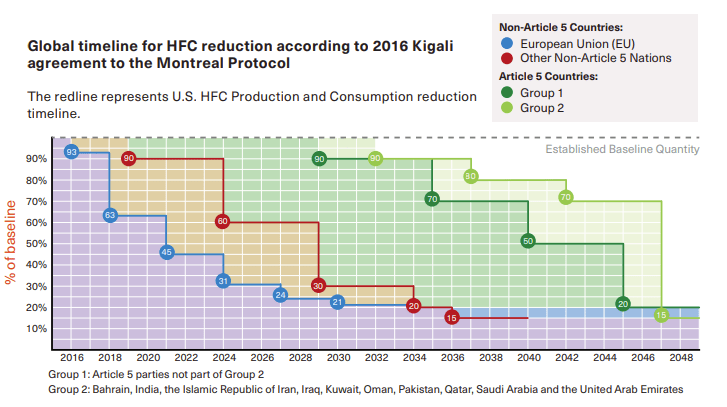
National and regional regulations restrict the use of high GWP HFCs
Regulatory timeline for US EPA proposal – United States and Canada
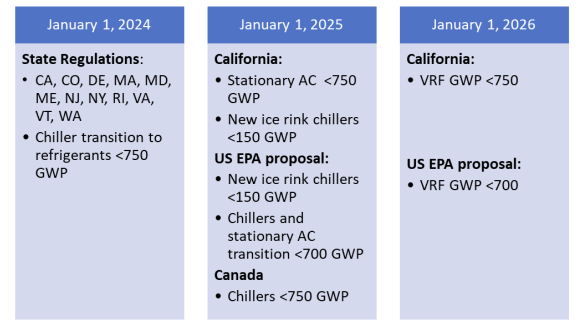
Codes and Standards Changes
Building codes are being updated by the latest safety standards which incorporate
requirements for the safe use of next generation refrigerants. The underlying safety standards are ASHRAE® 15 and CSA/UL 60335-2-40.
ASHRAE® 15-2019 adds new requirements for direct systems using A2L refrigerants. For
example, refrigerant detectors should be factory installed at the evaporator coil, quick
acting at low level, and increasing airflow to the occupied space with critical components
turned off. Also, the A2L refrigerant should be located away from ignition sources.
For indirect systems such as chillers, ASHRAE® 15-2019 adds more new requirements
with A2L refrigerants including similar requirements on refrigerant detectors for direct
systems, remote safety control sequence, and higher ventilation rate. It is also important
to note the multiport refrigerant detector can no longer be used for indirect systems with
A2L refrigerants.
Refrigerant Management Requirements
Section 608 of the U.S. Clean Air Act defines proper management of refrigerants used in
HVAC equipment, including maximum limits for fugitive emissions and proper handling
requirements during service and repair of the equipment. It continues to evolve, generally
with increasing stringency. EPA is expected to incorporate additional requirements for
refrigerant management in the AIM Act.
Future Availability
The U.S. EPA allows for the continued use of recycled, recovered and stockpiled supplies of all
refrigerants indefinitely, regardless of phase phase-down date.
Key Terms Defined:
ODP – ozone depletion potential – degree to which a substance can degrade the ozone layer;
all measurements relative to a similar mass of CFC-11, which is indexed at 1.0.
GWP – global warming potential – degree to which a greenhouse gas (GHG) traps heat in the
atmosphere; all measurements relative to a similar mass of carbon dioxide (CO2 ), which is
indexed at 1.0. The buildup of GHGs can cause climate change.
CFCs – chlorofluorocarbons (e.g. R-11, R-12) – phased out by the Montreal Protocol in 1996
because of their very high ODPs. Significant impact on both ozone depletion and global
warming due to the chlorine and fluorine atoms and very long atmospheric lives.
HCFCs – hydrochlorofluorocarbons (e.g. R-22, R-123) – also contain chlorine, but contribute
less to ozone depletion and climate change due to shorter atmospheric lives. Still in use
globally, but has phase-out dates scheduled under the Montreal Protocol.
HFCs – hydrofluorocarbons (e.g. R-134a, R-404A, R-407C, R-410A) – do not contain chlorine,
but they do have high GWPs given their fluorine content. Now being phased down globally
under the Kigali Amendment to the Montreal Protocol.
HFOs & HCFOs – hydrofluoro-olefins (e.g. R-1234yf, R-1234ze(E)) and hydrochlorofluoro-olefins
(e.g. R-1233zd(E)) – next-generation refrigerants that are non-ozone-depleting with ultra-low
GWPs and very short atmospheric lives (measured in days vs. years or decades).
HFO blends (e.g. R-454B, R-513A, R-514A, R-515B) – blends including an HFO. They feature
lower GWPs and, as they receive ASHRAE® classification and SNAP approval, are becoming
available for use in specific applications.
- Zeotropes (400 series blends) – have components that boil and condense at different
temperatures (i.e. have some degree of temperature glide). Lower glide is typically preferred for
HVAC applications. - Azeotropes (500 series blends) – behave like a single component refrigerant during phase
change, with virtually no temperature glide.
Montreal Protocol – an international treaty signed in 1987, originally designed to protect the
ozone layer by phasing out the production and consumption of ozone-depleting substances.
The Kigali Agreement was officially ratified in 2017 as an amendment to the Montreal
Protocol, and phases down the global production and consumption of HFCs beginning January
1, 2019. Individual countries must ratify the amendment for it to apply domestically.
SNAP – the Significant New Alternatives Policy of the U.S. Environmental Protection Agency
(EPA) evaluates refrigerants and classifies them as acceptable or unacceptable replacements
based on their overall risk to human health and the environment.
De minimis – lacking significance or importance; too trivial or minor to merit consideration
Considerations When Selecting Refrigerants
Choose the best refrigerant for each application based on a balance of safety (toxicity,
flammability, asphyxiation, and physical hazards), environmental impacts (lowest GHG
emissions) and total cost of ownership (energy efficiency of the entire system).
Flammability
With the transition to lower-GWP refrigerant
options, flammability has emerged as a new
variable for consideration, especially in higher
operating pressures.
In 2010, a new flammability category was created
within ASHRAE® 34. Subclass 2L captures
refrigerants with a Burning Velocity (BV) less than
10 cm/second and a high Minimum Ignition Energy
(MIE), indicating higher difficulty to ignite.
2L refrigerants have faced challenges in
application due to being governed as Class 2 refrigerants. Codes and standards
are now in the process of being updated to include requirements that reflect
the less flammable nature of 2L refrigerants compared to Class 2 flammability.
ASHRAE® 15 and ASHRAE® 34 were updated to reflect this change in 2019, and
UL 60335-2-40 was updated in 2017. These changes have been fully adopted by
International Mechanical Code (IMC).
Trane® is committed to offering non-flammable solutions whenever possible, and
the lowest possible flammability when slightly flammable solutions are required.
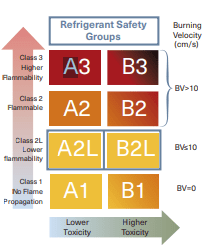
Toxicity
This is, perhaps, one of the most misunderstood properties of refrigerants. Specifically, it is important to distinguish between toxicity and safety; they are not the same. Because refrigerants displace oxygen, the greatest safety risk associated with all refrigerants is exposure leading to asphyxiation. Occupants are significantly less likely to be exposed to unsafe levels of low-pressure refrigerants because – in the event of a leak – air would leak into the machine rather than being expelled into the space.
ASHRAE® 34 classifies a refrigerant’s toxicity based on its occupational exposure limit (OEL). OEL refers to the time-weighted average concentration of refrigerant to which “nearly all workers can be repeatedly exposed without adverse effect” over the course of “a normal eight-hour workday and a 40-hour workweek”:
• Class A refrigerants have an OEL ≥ 400 ppm
• Class B refrigerants have an OEL < 400 ppm
R-514A has an OEL of 320 ppm. This means you should see no negative effect if you are exposed to 320 ppm of R-514A for 8 hours/day, 40 hours/week. For chiller applications, rarely do mechanical rooms see > 2 ppm, and this exposure typically occurs during servicing for very short periods.
To avoid confusion with building code definitions, ASHRAE® 34 was updated to indicate toxic, highly toxic or neither as defined in the International Fire Code (IFC), Uniform Fire Code (UFC), and OSHA regulations. None of the refrigerants shown in the table are considered toxic or highly toxic by the IFC, UFC, OSHA, or in the NFPA 1 (National Fire Protection Association) Fire Code.
Refrigerant Management Matters to Your Building Decarbonization Plan
Trane® is committed to reducing the potential environmental impacts associated with
refrigerants used in our products. We do this through:
- The EcoWise® portfolio of products with low-GWP refrigerants
- Intelligent Services, which monitor system abnormalities that could result in
refrigerant leaks - Mechanical Services, which include tracking refrigerant replacement and
completing the proper documentation for annual emissions reporting
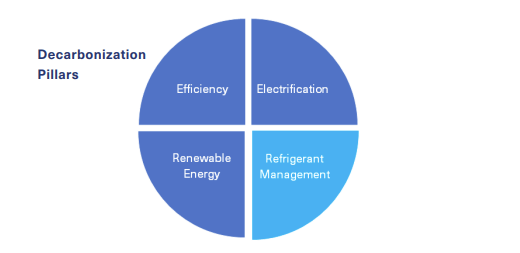
Refrigerant Choices
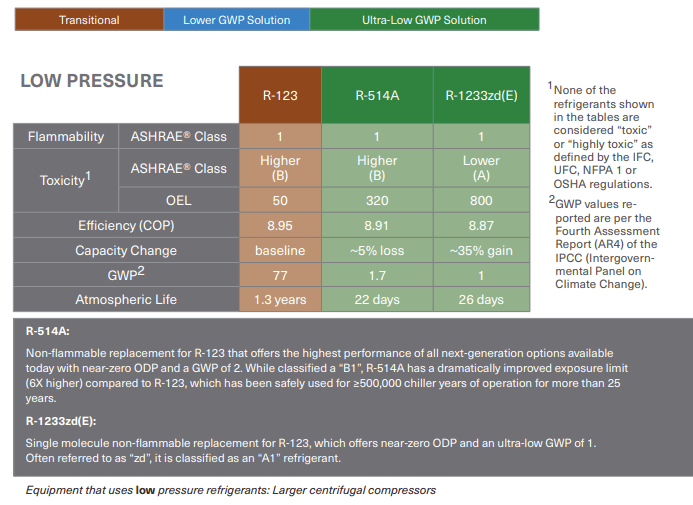
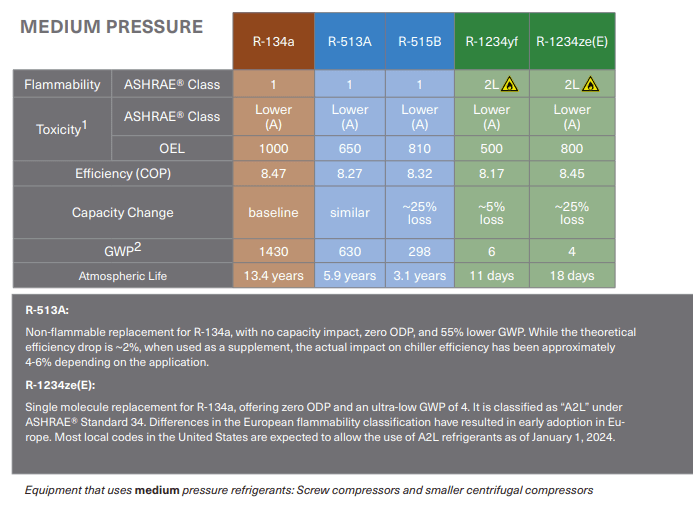
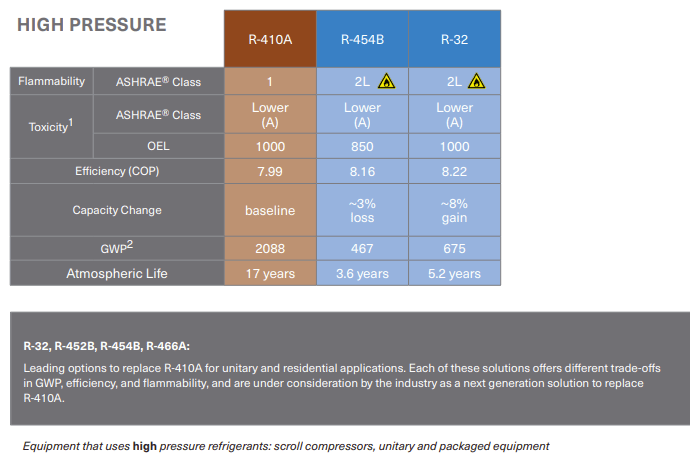
Trane – by Trane Technologies (NYSE: TT), a global climate innovator – creates comfortable, energy efficient indoor environments through a broad portfolio of heating,
ventilating and air conditioning systems and controls, services, parts and supply. For more information, please visit trane.com or tranetechnologies.com.
All trademarks referenced in this document are the trademarks of their respective owners